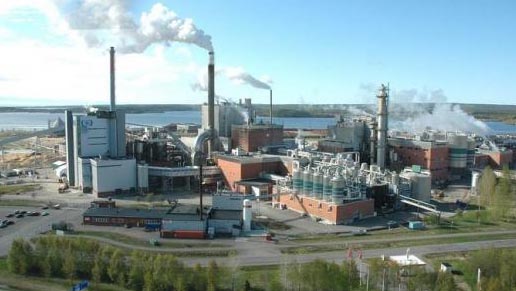
Veolia Water Technologies Inc. has been awarded a contract by Smurfit Kappa to supply state-of-the-art HPD ® systems at the Sangüesa mill in Northern Spain.
Smurfit Kappa is one of the world’s largest packaging goods providers and kraft paper manufacturers. Through its mill located in Sangüesa in the foothills of the Pyrenees in the northern Spanish province of Navarra, Smurfit Kappa provides the raw materials for producers of paper bags. Paper-based carrier bags provide a sustainable alternative to consumers’ use of plastic bags of which only less than 1% is recycled every year.
To increase its liquor treatment capacity and optimize the efficiency of recovery boiler operations, Smurfit Kappa Sangüesa has selected Veolia Water Technologies for the engineering, supply and mechanical installation of an HPD ® concentration and evaporation system resulting in an upgrade of around 30% of present operations.
“ Veolia has a history of success in providing solutions to the global Pulp & Paper market. The project for Smurfit Kappa Sangüesa is another example of the use of proven technologies to efficiently achieve increased operational capacity ” stated Klaus Andersen, CEO of Veolia Water Technologies Americas.
Critical to meeting the objectives of minimizing asset downtime, Veolia’s solution provided a forced-circulation low energy concentrator. Thanks to recent innovations in its design, this unit has minimal washing needs which create no disruption of production while achieving designed production rates. This competitive new design of the concentrator and peripheral equipment also addressed the need for a solution within constrained space requirements. With minimal recirculation piping, structural steel, and civil works, the concentrator has a reduced footprint that lowers overall site construction costs.
Veolia’s solution, which also includes two falling film evaporators with preheaters, condensers and a new vacuum system, will enhance the chemical recovery process by raising the liquor concentration up to 72% dry solids (virgin) to the recovery boiler while producing high-quality condensate for reuse leading to water conservation. The need for reduced energy consumption was also met through lower steam demands thanks to a design adapted to minimize fouling, foaming and scaling which increase heat transfer efficiencies in comparison with other alternative technologies.