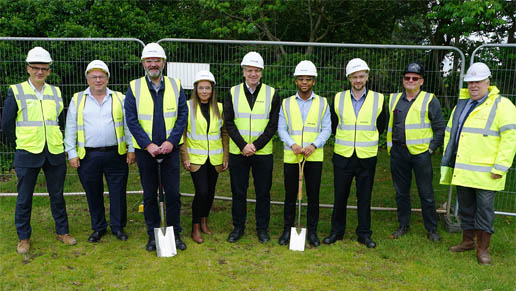
After more than 100 years at the famous Camp Hill site, Sulzer has started the process to move its facilities and create a new center of excellence for its customers. Sulzer’s brand new service center will be located at the prestigious Birmingham Business Park, where the company will base its UK head office as well as state-of-the-art repair and maintenance facilities.
Sulzer are working with Canmoor Developments Limited to deliver this important project, which will provide Sulzer’s customers with best-in-class service for electromechanical repairs as well as new high voltage testing facilities.
The 7’618 sq. m (82’000 sq. feet) purpose-built service center has been designed using 3D mapping technology that positions both the existing and new equipment in the most efficient layout. By optimizing the floor plan, material flow will be improved and project repair times for customers will be minimized.
The building phase is scheduled to be complete in early May 2020, after which there will be a carefully planned relocation of all the equipment, such as the copper rolling mill and coil manufacturing machinery, winding machines and the high voltage test bed. In addition to the existing equipment, Sulzer is also taking the opportunity to invest in a new high-speed balancing chamber, which will be located below-ground, and will be one of the most advanced facilities in Europe.
For the employees, the move will bring a brand new working environment along with better facilities and parking. Chris Adams, Coil Shop Operations Manager, comments: “The new service center will offer a host of improvements both for us and our customers. It is an exciting time for us and we are looking forward to moving in.”
Existing customers, who have visited the Camp Hill site, will appreciate the scale of the move; the amount of specialist rewinding equipment and machine tools alone will pose a considerable challenge. In addition, Sulzer is investing in modern IT infrastructure as well as new ovens and paint booths to provide high-quality finishes to repaired components.
Sulzer has developed a detailed plan for the relocation of each department that ensures customers will experience no downturn in service. Operations will be able to work between the old and new sites with the phased move taking place over two months. This will provide a seamless move and ensure that every customer has a smooth transition with Sulzer to the new site.
Chris Powles, Head of Electro Mechanical Services – EMEA, comments: “The aim is to create a new center of excellence that will operate on lean manufacturing principles and deliver an enhanced customer experience. This enables us to keep moving forward with technological advancements and invest in the future, for the benefit of our customers.”