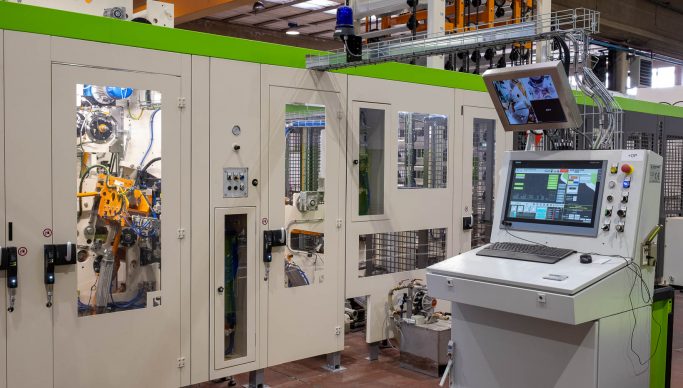
The Tissue market is constantly evolving. The uncertainty of the cost of pulp, the high competitiveness of the market, the upheavals created by the current pandemic open up new challenges to tissue producers and transformers who need to anticipate competition with distinctive products, in short time frames and while preserving margins.
To help manufacturers in this challenge, Körber (Fabio Perini) has decided to create Pivot Solutions, the new center of excellence for the Tissue business that combines all its skills in converting, the deep knowledge of embossing solutions of Engraving Solutions and Roll-Tec, combined with the ability to analyze machine data and the quality of the products of the Pivot laboratories.
The goal is to support customers in the development of new products, roll and folded, drastically reducing time-to-market and investment risk with a turnkey solution.
“Today Körber – comments Dario Giannini, Customer Product Innovation Manager – is able to support companies in the development of new products and in the improvement of existing ones, without necessarily interrupting their production lines. With Pivot Solutions our customers will be able to test new prototypes or optimize the characteristics of existing products through the production of small batches, replicating, if necessary, the production conditions. Körber specialists, through the analysis of the pilot line data, will be able to help the customer develop the solutions that best suit his needs, identifying the best combination of paper, technology and characteristics of the finished product “.
Pivot Solutions is “glocal”, with a local presence at plants around the world and a global knowledge of the tissue market, thanks to the experience and interaction between the plants. Pivot Solutions today has five pilot lines, including the new Constellation™ S6 Pilot line and three Pivot laboratories, located between Green Bay, Lucca, and Joinville.
“In the center of Lucca – continues Dario Giannini – the first Pilot line was installed with the innovative Constellation™ S6 four-roll technology, capable of producing products at a production speed of up to 700 m/min”. This new pilot line is equipped with our most advanced technologies, such as:
- Defender, a technological upgrade capable of producing over 10 thousand face masks in rolls per minute, the line is complete with a box filler machine to pack the rolls of masks into convenient boxes / dispensers;
- Motorized “Punzoncini”, where the elimination of pneumatics allows for a stable, precise, robust system, controlled directly from the HMI panel;
- Warm Up, the new embossing system that uses heating on the engraved steel roll to enhance the characteristics of the finished product, launched thanks to the collaboration with Roll-Tec;
- SAM, the intelligent control system capable of measuring the weight, consistency and diameter of the produced log, without compromising the production speed;
- Leonardo, a lotion station able to finely control the quantity of lotion applied by means of a special anilox roll in contact with the paper sheet;
- Glue filter, a technical modification that allows you to separate the fiber from the glue, allowing the clean glue to return into circulation;
- Aquabond, the glue-free lamination system that allows you to use water instead of glue to join paper plies.