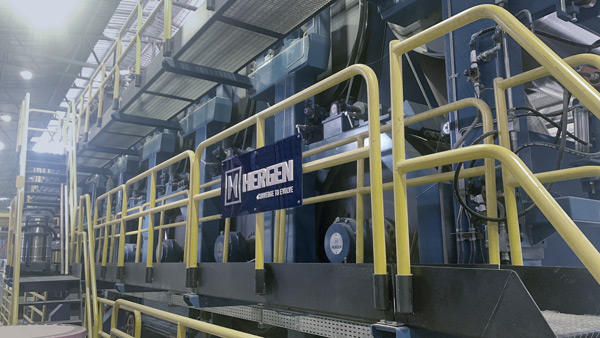
Being the largest manufacturer of paperboard in Latin America requires overcoming the daily challenge of delivering value to the customer. Therefore, the Brazilian core board producer INCAPE works tirelessly to exceed expectations and provide the best experience to all its stakeholders.
In late 2021, the company contracted with the machinery manufacturer HERGEN for its largest project modernization project, and now celebrates the achievement of this memorable challenge in record time.
To accomplish this historic machine stoppage, it took exactly 132 hours, more than 100 people directly involved in disassembly and assembly, and more than R$37 million invested.
“Over the past five years, we have been constantly investing in new technologies, always seeking to deliver value to our customers. However, this specific project became a milestone within our company. The resources dedicated to a single project and the level of involvement required from the INCAPE team with the suppliers was unprecedented. It required a lot of dedication and unparalleled commitment from everyone, because we knew that to deliver everything that was proposed in a timely manner, we needed to excel in all aspects,” says Thiago Karam, General Supervisor of INCAPE.
The project relied on the support of excellent professionals and the best suppliers in the market to reach the five-day mark for the replacement of the entire paper machine. The entire team came together in favor of a single goal: to offer the tissue market an industry even more specialized to what it proposes, delivering efficiency and cost reduction to the conversions.
“To our customers, we would like to inform that the constant evolution of the industrial park is due to the incessant search for reducing costs in the converting lines. INCAPE’s R&D pulses all the time in search of solutions for the tissue industries. We conduct the company with the purpose of delivering value to the customer and solving their pains,” adds Thiago.
In order for the Drying Project to be carried out in such a successful way, INCAPE managed and planned all the stages and processes in detail. The frequent meetings with the team and suppliers involved in the process, in addition to the risk assessment and contingency plan to mitigate failures, contributed to a smooth and uneventful execution.
“The commitment of everyone, aligned to a high performance project, made the success of this stop and placed INCAPE among the large companies that use the most advanced technologies in equipment, controls, and safety in paper manufacturing, consolidating itself as the largest and best manufacturer of special papers in the market”, declares Paulo Vito, Project Engineer at INCAPE.
TECHNICAL DETAILS
The Drying Project consisted in replacing the entire drying battery (drying cylinders), the installation of new structures to accommodate the new cylinders, new passageways suitable to NR12 standards, the system of passing the tip by ropes, a new winding machine, an automatic system for turning the jumbo jets, a supervisory for monitoring and more assertive interventions in the production process, and a new production management system for monitoring downtime, breaks and operating costs.
“It was an innovative and challenging large scale project, a set of activities performed by the group aiming at a common goal: the execution and delivery within the estimated time. It was almost a year of studies, ideas and changes in relation to the initial project, divergences found, the fact of removing the old equipment and installing the new one in the same place, reduced physical space, high demand of work, knowing how to deal with several areas and people with different profiles was an essential task to achieve the objective”, points out Argélio Faria, Mechanical Maintenance Supervisor at INCAPE, about the challenges found in the process.
These challenges were completely overcome and Argélio believes that “this was the result of good planning, perspective and analysis of possible failures and interferences. The success of this challenge was due to the empathy among the teams; merit to each trained professional who participated.
RESULTS
“In a short period of time, the results have been better than projected – the result of all our preparation and strategy throughout 2021. Our operation team has been doing a great job and showing an incredible capacity to adapt”, says William de Souza, INCAPE’s Industrial Manager.
The new facilities, besides being safer for the collaborator, also present excellent results for INCAPE’s customers, since now the company will be able to supply larger demands through the great reliability established with the automation of the new installations.