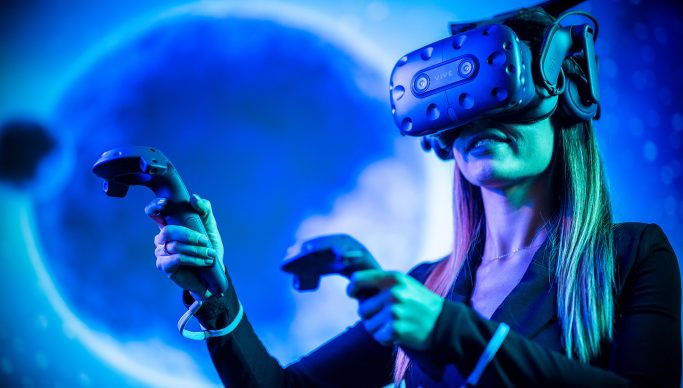
The German group LEIPA is the world’s first paper mill to employ virtual reality (VR) from Voith as a modern and immersive training method. At its Schwedt site located on the Polish border, the company trains its employees extremely effectively using the VR system. To perform the installation in spite of the contact restrictions imposed as a result of the coronavirus pandemic, Voith and LEIPA drew on a new tool for remote video support: On-Call.Video. LEIPA has been using this audio-visual communication system with wireless data glasses since January 2020.
With the VR application, LEIPA employees can complete hands-on training in the computer-generated environment at any time and without any danger. From simple exploration of a paper machine for newbies to the complex process of changing the press sleeve on a modern shoe press, the system offers every employee a completely new training experience. This is made possible by 3D visualization in a headset combined with control devices for the interaction. The employee can move freely in the virtual reality setting and is guided through various tasks step by step.
Specifically, for the VR training from the Voith PaperSchool, LEIPA set up a futuristically designed room, the “LEIPA Virtual Reality Center,” at the Schwedt location. A special design and lighting concept underscore the modernity of the VR technology. Voith also supplied a touchscreen and wireless VR equipment to meet the special customer request for a cable-free studio.
How the OnCall.Video remote video support tool can increase efficiency and thereby give customers traceable added value became clear with this start-up. “The room was already prepared and the sensors attached,” recalls Patrick Dengel, Digital Tools Manager at Voith. “We handled the details via OnCall.Video. To accomplish this, the glasses were integrated into the LEIPA WLAN, via which a video and audio connection to the Voith experts in Heidenheim was established.” Without the remote connection, the VR system would not have been functional as quickly.
OnCall.Video offers LEIPA clear advantages especially for problems in the production flow, because the papermaker can draw on know-how outside the company to find solutions with virtually no delay and with cost savings. “Required expert knowledge is not always available on site, so integration of external know-how is that much more important,” stresses Patrick Dengel.
“In principle, I can guide everything with the tool,” adds his colleague Stefan Endras, Product Manager, OnCall.Video. “Our main emphasis is on quickly connecting the customer with the experts. In this way, we can also partially compensate for the lack of skilled workers.” However, added value is also offered to the customer through the fact that various locations can easily be connected to each other and, as a result, internal exchange of specialized information and knowledge transfer are promoted.
With the virtual reality solution and OnCall.Video, LEIPA underscores its digital competence. “Which papermaker can claim to have the most modern media in use before anyone else?” argues Senior Manager Steffen Deszpot. “Industry 4.0 has already arrived here – and we are happy to show it.”