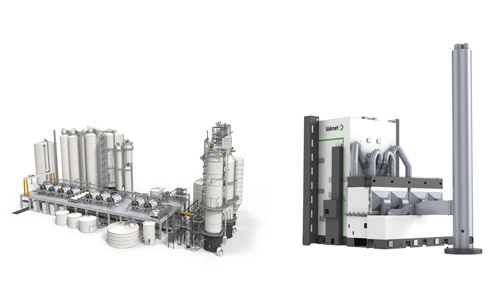
Valmet will deliver key pulp mill technology to Shandong Sun Paper’s new Yandian pulp mill in the Shandong province in China. Valmet’s delivery includes cooking and fiberline, a recovery boiler, and ash crystallization. The scope also includes analyzers and measurements for fiber line as well as an optimizer and safety related systems for the recovery boiler. The new mill will produce 600,000 tonnes of pulp per year and is scheduled to start up during the last quarter of 2026.
The order is included in Valmet’s orders received of the second quarter of 2025. The value of the order will not be disclosed.
“Valmet has been a trusted partner for our recent chemical pulp lines. The previously delivered technologies to Beihai have proven high-availability and efficient utilization of raw materials. Valmet team has constantly supported our targets to secure the successful outcome of our projects. This is the third cooking and fiberline delivery and second recovery boiler delivery from Valmet since 2020, and we are confident in yet another successful project with them,” says Zehua Liu, General Manager Sun Paper.
“Sun Paper has trusted our cooking, fiberline and recovery boiler solutions for several of their recent pulp projects. With excellent collaboration we were able to create a concept to answer our customer’s needs. With our strong local presence in China and competitive technology and services solution, we are able to deliver this project successfully even with the tight project schedule,” says Sami Riekkola, Business Area Executive Vice President, Pulp Energy and Circularity, Valmet.
“We are very happy to continue our excellent cooperation with Sun Paper in this strategic investment. In addition to previous pulp, paper, and automation technology deliveries, we also have extensive services cooperation with the customer. In this project, our Chinese teams will play a key role in engineering, procurement, project management and offering site services to the customer,” says Xiangdong Zhu, Executive Vice President, China, Valmet.
Technical information about the delivery
The cooking and fiberline will feature leading process technology, including the latest developments of Valmet Continuous Cooking technology, to reach excellent efficiency in energy and raw material utilization. A high end-product quality with low effluent flows and high environmental performance will be secured with the latest generation of Valmet TwinRoll wash presses throughout the fiberline in combination with Valmet´s screening, oxygen and bleaching technology. Valmet Fiberline Analyzer and measurements for fiberline control are also part of the delivery. The fiberline will have a capacity of 600,000 tonnes per year.
The delivery for the recovery island includes a Valmet Recovery Boiler and Ash Crystallization. The high-power recovery boiler is designed for long lifetime and long campaigns between cleaning shutdowns. The boiler will have a capacity of 3500 tonnes per day. The high-power features will enable higher renewable electricity production for mill’s own use. The ash crystallization secures efficient removal of chloride and potassium from the mill chemical cycle, which reduces corrosion and helps to minimize emissions. Valmet Recovery Boiler Optimizer and safety related systems for the recovery boiler are also part of the scope.