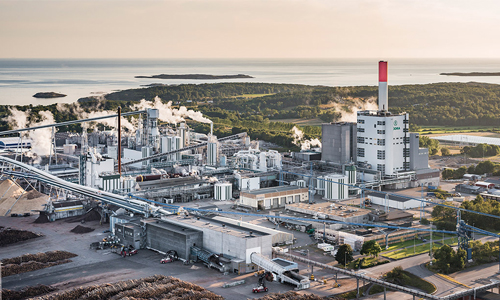
Swedish Södra Cell Värö is one of the worlds most modern and largest producers of NBSK pulp, with annual output of 700 000 ton. Södra is leading in circular economy and sustainable production, something that is also reflected in the long-term relation that Södra Skogsägarna keep with their forests. In addition to renewable pulp, the mill also contributes with renewable heat for the district heating grid of nearby city of Varberg.
During 2020 the decision was made to increase pulp production to 780 000 ton/year. In the framework of the project called Expansion 2.0, Heat Management will supply the cost-efficient solution for sustainable and energy efficient steam sootblowing for the pulp mill recovery boiler. Heat Management was chosen as the supplier, given their solution uniquely offers both substantial steam savings and the ability to double the sootblowing capacity. This dynamic sootblowing is ideal for meeting the demands associated with productions increases, regarding both predictability and sustainability.
From a tight cooperation between Värö mill and Heat Management, a specific solution was developed that will materialize in a seamless integration of Heat Managements patented solution HISS™ in the mill DCS system. Sootblowers are operated continuously to keep the flue gas pass clean and to prevent fouling from sintering on heating surfaces. In many cases the existing amount of sootblower starts per day is not enough, resulting in limited production or outages for manual cleaning. HISS™ will increase the sootblowing capacity by 100 % without installing more sootblowers or steam headers, while improving real-time digital diagnosis and energy efficiency of the already installed sootblowing system.
The project scope includes continuous dialog for validation and verification, with weekly and monthly studies of process data to reveal how the additional sootblowing capacity shall be distributed in the recovery boiler, in order to achieve an efficient production on a higher and more sustainable level.