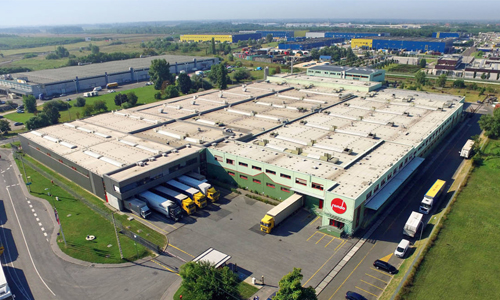
BOBST helps its customers with improving the productivity of their machines. The concept of process optimization covers all areas of production, resulting in performance increases of up to 150 percent per order. This is demonstrated by the pilot project recently carried out at Rondo in Budapest. The renowned corrugated board packaging company and its customers benefit from the efficiency increases of their MASTERLINE 1.7.
The call for higher throughput, shorter setup times, lower operating costs and improved quality is omnipresent in the printing industry. Everyone wants it: printing customers and printing service providers alike. In order to help its customers increase productivity, BOBST has launched a new program that allows them to put their production processes to the test. The concept of process optimization is a service offered by the machine manufacturer to improve the productivity of BOBST machines. Qualified BOBST technicians carry out a thorough analysis of all process steps at the customer’s premises in order to identify areas where there is room for improvement.
BOBST’s expert technicians do not only assess the presses, but rather takes the entire environment into account in their evaluation. Among other things, this includes tooling, operator knowledge, safety in the workplace, machine condition, job layout and many more. The findings and recommendations of this analysis are included in a report, which BOBST uses to put together a tailor-made action plan. This shows how customers can improve the productivity of their production line. The highlight here is that, if the customer decides to use BOBST for the entire process optimization, BOBST guarantees the achievement of productivity targets set for specific jobs which are chosen by the customer. At the end of the process optimization, the results are recorded through acceptance tests and a compensation is issued should the results not meet the expected targets.
“BOBST sees process optimization as a true partnership between a machine manufacturer and printing house. We provide customers with the expertise and experience of our highly qualified technicians and help them to increase their effectiveness,” explains Arnaud Jolliet, Product Development Specialist Business Unit Services at BOBST.
Exceeded expectations
One of the first customers with whom BOBST successfully implemented this performance-oriented form of process optimization is the corrugated packaging company Rondo in Budapest – the Hungarian location of Rondo-Ganahl AG, the traditional Austrian corrugated board and packaging manufacturer. During the six-month project period between March and September 2019, a MASTERLINE 1.7 printing line with three flexo units was optimized there. In the agreement on objectives, the aim was to improve output performance on the basis of three specially selected reference orders. These orders were a pizza box, hazardous goods packaging and chips packaging – all corrugated board packaging with different requirement profiles as is often the case at Rondo.
“The cooperation with BOBST during the project period ran flawlessly, and the results we achieved have significantly exceeded the original output level. They even exceeded the objectives set out in the action plan. We certainly weren’t expecting that! In the case of the hazardous goods packaging, the net output increase reached almost 150 percent, while the performance of the other two reference jobs increased by 50 percent (chips) and 100 percent (pizza box),” says Tamas Gaszmann, Technical and Production Manager at Rondo in Budapest.
The process optimization measures implemented by Arnaud Jolliet and his team included software updates, training of machine operators, adjustment of the flexographic units, improvement of the register and further improvements to the tools. Over the years, the orientation of the rollers within the flexographic plants had shifted. They were reset and returned to their original position. This has helped to reduce setup times and improve quality. In the case of the vacuum settings for sheet transport, it was found that unplanned machine downtimes could be reduced by targeted employee training. Many other improvements to various tools served adapt them to higher speeds: for example, using soft rubber instead of hard rubber, an increased number of nicks and new layouts designed to reduce waste, which ultimately made palletizing easier. Most recently, the MASTERLINE was equipped with BOBST Connected services – which constitutes a major advantage for remote production monitoring.
Future projects
BOBST currently offers the process optimization program in Europe and North America. In 2019, BOBST started about 30 process optimizations – most of them have now been completed and some are still ongoing. This project will also continue at Rondo in Budapest. “We are planning further optimizations with BOBST as well as additional training for our employees. The positive outcome of the first process optimization convinced us to continue along this path,” concludes Tamas Gaszmann.