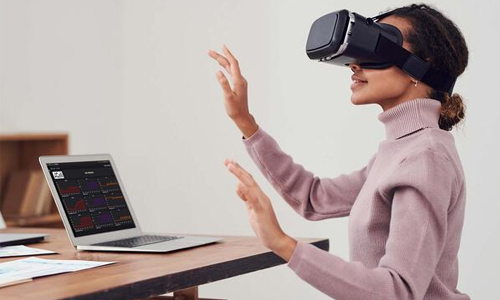
There are many tools in the modern digital age capable of increasing the efficiency of businesses operations, personalizing the communication with workers and customers and ensuring an advanced and streamlined interaction between humans and machines. Two of the most recent tools to be adopted by the manufacturing industry are chatbots and augmented reality (AR).
How Chatbots and Augmented Reality work
Chatbots are communication softwares that allow the interaction between man and machine by using natural language thanks to a so-called conversational interface, eliminating the need of interaction through programming languages. These softwares are therefore able to understand users’ questions and respond accordingly.
Augmented reality is a technology that allows workers, thanks to the so-called overlay, to “enhance” the real world field of view by superimposing data, information, and diagrams onto it by using smartphone and tablet displays or wearable devices such as head-mounted displays (HMD).
The role of Chatbots and Augmented Reality
The chatbot market is expected to reach a staggering $1.25 billion worldwide by 2025. Chatbots have been used until now usually for customer support, allowing companies to connect more easily with clients 24/7, but they can also be used by the manufacturing sector to:
- manage supplies and inventory;
- aid with order fulfilment and delivery;
- simplify supply chain communications;
- enable maintenance crews to check the conditions of machinery and equipment in the workplace;
- facilitate maintenance crews operations.
The augmented reality market is also booming and is expected to grow to nearly $19 billion worldwide by 2024. This technology is being used to:
- train plant workers;
- improve worker productivity during machine installation, monitoring, and troubleshooting by providing them with real-time information so they can make adjustments/changes as they work;
- improve the product design process by providing a visualization of the product in context and collaboration between parties that are separated geographically;
- facilitate inspection and maintenance.
As we can see the many uses of chatbots and augmented reality can help a company significantly improve overall operations, product quality and, ultimately, profits.
Chatbots and AR in Industrial Maintenance: the main benefits
These two technologies allow workers to gather information quickly and test maintenance scenarios, all while working directly with the machine. The benefits of using chatbots and augmented reality in industrial maintenance are many, including:
- fewer human errors;
- faster execution of maintenance and repairs;
- fewer machine breakdowns;
- less machine downtime;
- reduced maintenance costs;
- improved operational speed and productivity;
- better regulatory compliance;
- higher profits.
With that in mind, let’s take a closer look at how chatbots and augmented reality can achieve these goals.